Table Of Content
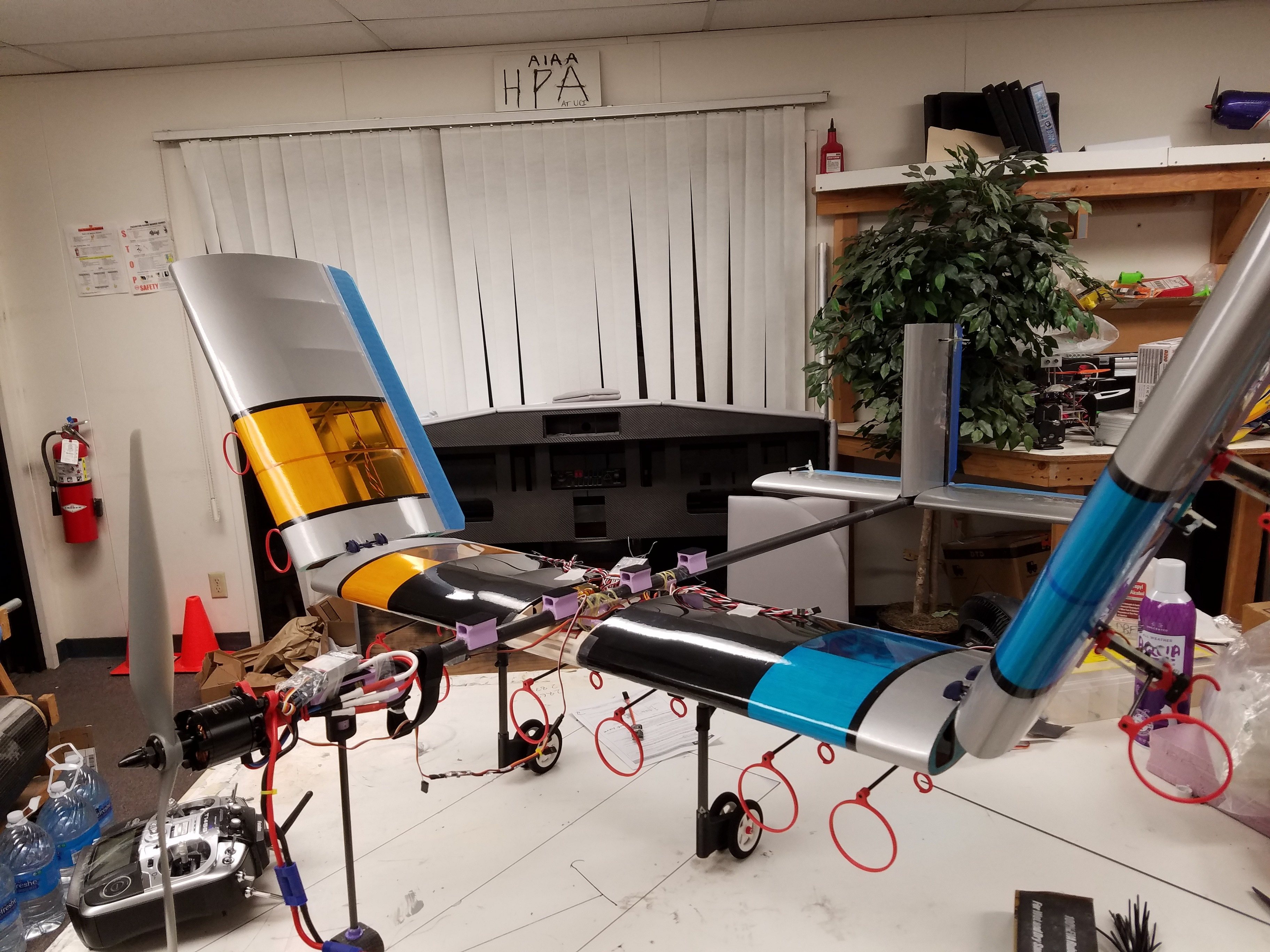
In order to minimize the number of speed controllers used on the aircraft, which adversely affects theRated Aircraft Cost (RAC), a single-motor configuration was chosen. To minimize the number of servosneeded and reduce the complexity of the control system, the aircraft's only control surfaces are rudderand elevator. The wing has substantial polyhedral to aid controllability and eliminate the need for rollcontrol.
food
Students working with the team will develop skills with products that will carry over to their professional careers. DBF gives students the opportunity to explore a variety of disciplines within aeronautics and apply what they learn in classes in a setting similar to that of industry. The packages were also equipped with shock sensors that nullifies the score of a deployed package if tripped. Unfazed by the challenges and adversity, the team managed to successfully deploy 6 packages, the third most of 97 teams, and scored the highest finish of 9th, marking the return to competitiveness. During the fall quarter, 2021, we finished our preliminary design of our aircraft including the fuselage, wings, tails, and landing gears.

USU Scientists Among Multi-Institution Team Receiving NASA Achievement Award
A biplane configuration was chosen in response to the size factor of the Rated Aircraft Cost (RAC).Having two wings allowed the wingspan to be reduced, lowering the contribution to the RAC from the Ydimension parameter. Larger tail surfaces were selected to reduce the nose to tail length, lowering the Xdimension contribution. We are a team of undergraduate and graduate students at MIT that develop aircraft for the annual AIAA Design/Build/Fly competition.
2024 Competition
To minimize aircraft weight and size, the rear wingdoubles as a horizontal stabilizer. The aircraft has two vertical stabilizers to achieve a simple foldingmechanism while maintaining symmetry. All aerodynamic surfaces fold along the fuselage to transitionthe aircraft from the flight condition to the stowed condition. Together, a belly skid and tail guard ensure safe landings while minimizing thesize and weight of the aircraft.
AIAA Announces 2024 Design/Build/Fly (DBF) Competition Winners
Recent mission requirements have included increased focus on fuel efficiency, environmental sustainability, and electric propulsion. Additionally, the use of advanced materials and manufacturing techniques has become more prevalent in the competition, as students look for ways to optimize their aircraft performance while keeping costs down. In order to minimize the diameter and length of the stowed condition aircraft, a single-motor, tandem wingconfiguration with a folding propeller was chosen.
Contents
The American Institute of Aeronautics and Astronautics Design Build Fly (AIAA DBF) competition is an annual aircraft design competition. Each year students are tasked with designing, building, and flying unmanned, electric powered, remote control aircraft. These aircraft are required to meet unique and very specific design requirements and mission profiles. Each year the missions change forcing teams to come up with completely new aircraft year after year. Student teams will design, fabricate, and demonstrate the flight capabilities of an unmanned, electric powered, radio controlled aircraft which can best meet the specified mission profile. The goal is a balanced design possessing good demonstrated flight handling qualities and practical and affordable manufacturing requirements while providing a high vehicle performance.
Utah State University Students Excel at National Aviation Maintenance Competition
Our students gain experience in conceptual design, multidisciplinary optimization, aerodynamic, structural and propulsive analysis, composite layups, CAD software, UAV fabrication and RC flight. DBF provides a means for our members to develop their technical, collaborative and communication skills while exploring their interest in aeronautics. DesignBuild Fly is a 5,000 square foot highly-interactive STEM exhibit, blending learningoutcomes based in both process and content of airplane design andmanufacturing. Visitors learn the toolsand practice the methods that aircraft designers, engineers and builders use, whileexploring a variety of interesting features of actual aircraft design andfabrication. The objective was to design, build and fly an airplane to demonstrate Urban Air Mobility missions, such as medical transport and urban air taxis. Design Build Fly is a student organization focused on creating novel remote controlled aircraft to compete in SAE Aerodesign and AIAA Design Build Fly competitions.
INCLUDES FIREFLY'S
You can find/compare rules, review contest results, and access the Top teams' reports for a particular contest. The aircraft needed to carry both internal cargo as well as external, deployable sensors. A team from USU's aviation program had an impressive showing at the recent National Aviation Maintenance Competition in Chicago.
UC Merced Drone Team Soars to New Heights in Global Competition Newsroom - University of California, Merced
UC Merced Drone Team Soars to New Heights in Global Competition Newsroom.
Posted: Mon, 17 Jul 2023 07:00:00 GMT [source]
We also focused our conceptual design of the aircraft based on the scoring analysis, which led us to decide a particular mission to focus our design upon. Along with the design, we made plans for prototyping/manufacturing and testing, which we are conducting in the current quarter, Winter 2022. Ultimately, the goal is to design and build an aircraft that will complete all mission requirements and earn the best overall score by finding the best scoring combinations of the missions. Design, Build, Fly is an annual competition hosted by the American Institute of Aeronautics and Astronautics (AIAA).
This is a timed mission for the ground demonstration of flight mission 2 and flight mission 3. A crew member from the team will start from a start/finish line, load the full mission 2 payload, and will go behind the start/finish line. Then, the crew member will start again to remove the mission 2 payload and install the mission 3 payload, while finally coming back to the start/finish line. We build, prototype, and flight test from October through March, and compete with our final plane in April. Each team offers members the opportunity to obtain experience inwork of their individual fields of interest and manages a design step or subsystem(s)critical to the design and fabrication of an aircraft. We’re looking forward to getting your custom food truck, concession trailer or experiential marketing vehicle on the road!
The fuselage has a hinge onthe top skin just behind the nose to allow the payload compartment to swing open for easyloading of the passenger payload and easy dumping of the water payload. The aircraft weighs less than 1.5 kg empty,which is achieved through a combination of composite structures. The fuselage is a custom-molded sandwich panel; this provides a very light but strong structure that can carry the payloads. The airframe is supported by a carbon fiber tube that extends from the frontof the payload compartment to the tail.
Fromthe initial concept rendering, Design Build Fly has been envisioned as anexhibit built with and among a large number of authentic airplanesections. This required extensivecoordination between suppliers, EP and Roto, from early design through allstages of engineering and fabrication. The primary design objective for this year was to accommodate a random payload combination composed of passengers and cargo pallets.
Teams were assigned payload manifests at random and scoring was based on performance during these runs. The UW successfully design, built, and flew “The Growler”, a unique bi-plane configuration with high speed and payload capacity. The aircraft must complete three laps within a 5 minute flight window for this mission. In order to minimize the number of sub-assemblies of the Production Aircraft (Tony), which adversely affects theRAC, a single sub-assembly design was chosen and built.
Teams then competed in various military themed missions and as usual, the total score was a product of the flight scores and written report scores. The UW DBF team participated with the “Puget Sound Barrier” and placed within the top 1/3 of competitors. The UW design, built, and flew a “Joint Strike Fighter” aircraft with internal payload capability. The competition consisted of missions involving short take-off and landing, stealth missions, and strike missions. The “DawgAir 313” was designed to meet these design requirements using a unique morphing wing technology.
Located in Los Angeles, California, our fabrication facility is a one-stop shop to design, build, wrap, and repair your mobile business. Financing keeps more cash in your pocket now while you’re getting your new mobile business up and running. Lease a food trailer or get a food truck loan through one of our trusted financing partners. For over a decade SoCal Contractor has been one of the best luxury home builders in Southern California. The company has a Houzz ranking of #1 for four years in a row for the Southern California region. The President of the firm, Roy Yerushalmi, is a second-generation builder and a graduate of the Construction Management Program at the University of Houston.
To provide roll control, the vertical control surface is bisected and controlled independently to create rudderons. Since the center of mass is at a high elevation compared to the width of the landing gear, the aircraft uses a quadricycle configuration to maintain stability during takeoff and landing. A mathematical formula outlined in the rules calculates each entry's score, which lately combines design report and performance scores from fly-off missions. So it was natural for its hometown science center, Exploration Place, to choose aircraft design, engineering and manufacturing as the theme for its new signature STEM exhibit gallery. Teams were tasked with designing an aircraft for back country operations such as medical transport, cargo delivery, and rough runway operations. The UW’s “Dawg Sled” was manufactured using novel techniques such as 3D printing and composite structures.
No comments:
Post a Comment